ROBAM and HuazhongCNC Jointly Build 5G Smart Factory for Kitchen Appliance Manufacturing
ROBAM is an enterprise specializing in the development and production of kitchen appliances such as range hoods, steamers, gas stoves, disinfection cabinets, dishwashers, etc. It has been focusing on inheriting and innovating the essence of Chinese cooking culture for 42 years. ROBAM has been one of the world’s best-selling brands of range hoods and built-in cookers, and has been ranked among the top 500 Asian brands for 15 consecutive years.
Black Light Factory of ROBAM – 5G Smart Factory
When the workers of various manufacturing factories are working overtime in a hurry, the Hangzhou production base of ROBAM is extremely calm. In the sheet metal stamping workshop which is of tens of thousands of square meters, 284 sets of automation equipment are running on their own. It is the black light factory of ROBAM.
The production concept of “robot substitution” is not a whim of ROBAM, but a solution based on the difficulty of recruiting workers. ROBAM was established in 1979. After 42 years of development and technology precipitation, it has transformed from traditional manufacturing to a digital production workshop, and has successfully built a benchmark factory in the kitchen appliance manufacturing industry.
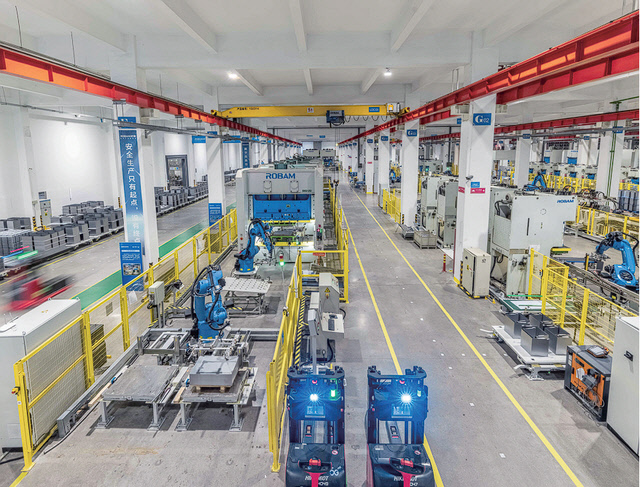
“Since 2012, this sheet metal stamping workshop has tried intelligent manufacturing upgrades, replacing some equipment with industrial robots. In 2016, the automation level of the workshop reached about 70%, and the new version delivered at the beginning of this year reached 100%. We have truly achieved the unmanned operation, the lights are usually turned off, so we usually call it a ‘black light factory'”, said by Ye Danpeng, the CMO of ROBAM. “Intelligent manufacturing upgrades are not achieved overnight, but are gradually iterated on the original basis. On the basis of the multi-party cooperation between ROBAM, Alibaba Cloud and HuazhongCNC, we successfully build an intelligent manufacturing base covering an area of about 50,000 square meters, and has built the first ‘black light factory’ in the kitchen appliance industry.”
On fume hoods production line, the flat steel plates go through “punching”, “shaping”, “cutting” and other links to be made as the finished products. And then, the finished products are placed on a flatbed car. When the car is about to be full, an AGV car slowly approaches and stops in front of the robotic arm, and sends out flashing “photoelectric signals”, at this time, the industrial robotic arm gets the signal content and stops the operation immediately and waits for the AGV trolley to tow away the flatbed truck which is neatly filled with finished smoke hoods, then the robotic arm turns around to continue the operation on the assembly line.
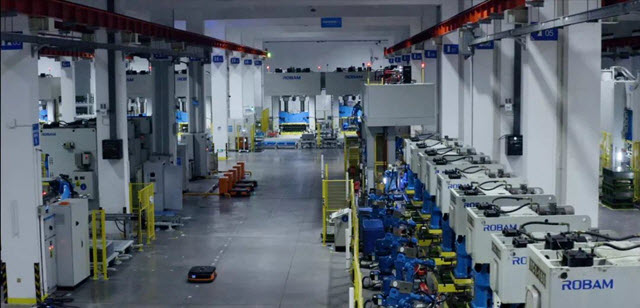
In fact, the trolley may go to fetch raw materials for the production of fume hoods, deliver finished products, or support the material delivery of other lines… Its path depends on the “system commands” received in real time, and it travels throughout the workshop. Similarly, when the robotic arms on the production lines suck the product, turn around, place material and etc. are all determined by the “system instruction” received. This system seems like the nerve center of the human body. Behind them, there is also a common brain” that performs complex calculations in real time and issues various task instructions. The “fume hood stamping and forming” production line is only a very small production link in the 50,000-square-meter workshop where it is located. According to statistics, this workshop has a total of 284 sets of automation equipment, tens of thousands of “data points”, 16 production lines and 27 AGV trolleys…
Compared with the traditional busy production line, it has few people on the smart production line. The machines “exchange information” and “produce” in an orderly manner. Since there are almost no people in the smart factory, the brightly lit scene in the factory no longer exists, and it even becomes dim. People who have visited the factory have given a unified name – “Black Light Factory”.
Robotic Production Enhances Management and Production Efficiency
“Black Light Factory” is the “Future Factory” created by ROBAM. In the definition of ROBAM, the “Future Factory” applies digital twin, Internet of Things, big data, artificial intelligence, industrial Internet and other technologies to factory production and sales, so that these factories can achieve innovative development such as intelligent production, intelligent management, and collaborative manufacturing.
In the case of difficult recruitment, ROBAM finally started to robotize the production lines. Before the completion of the “Black Light Factory”, 238 front-line workers were required to work in two shifts. After completion, only 33 workers are needed. The work content of workers has also undergone earth-shaking changes, becoming technical blue-collar positions such as “operation and maintenance engineer”, “equipment maintenance engineer”, and “system development engineer”.
Simultaneously with the robotization of the production line, the internal information system of ROBAM has been gradually changed from CRM to ERP, and finally to MES system. The construction of these systems has enabled ROBAM to initially capture and transparentize the data at the bottom of the factory. The purpose is to improve the yield rate in the production process and improve the overall operation and management efficiency. Today, all equipment in this 5G smart factory can operate on its own based on data and algorithms, production efficiency has increased by 45%, production costs have been reduced by 21%, and the yield has increased from 98% to 99%.