3C Industry Automated Production Line Applications
Empower the 3C electronics industry and build a Bluetooth headset smart factory!
Bluetooth headsets have always been a popular electronic product among people of all ages. The future of Bluetooth headsets is bright. The introduction of intelligent production lines for Bluetooth headsets can reduce costs and increase efficiency, helping manufacturers achieve good results in the competition!
In recent years, HSR Robotics has built an intelligent production workshop based on intelligent manufacturing and information technology for a large electronics manufacturer, which has greatly improved the company’s production!
01 Robot loading and unloading: mainboard tin loading
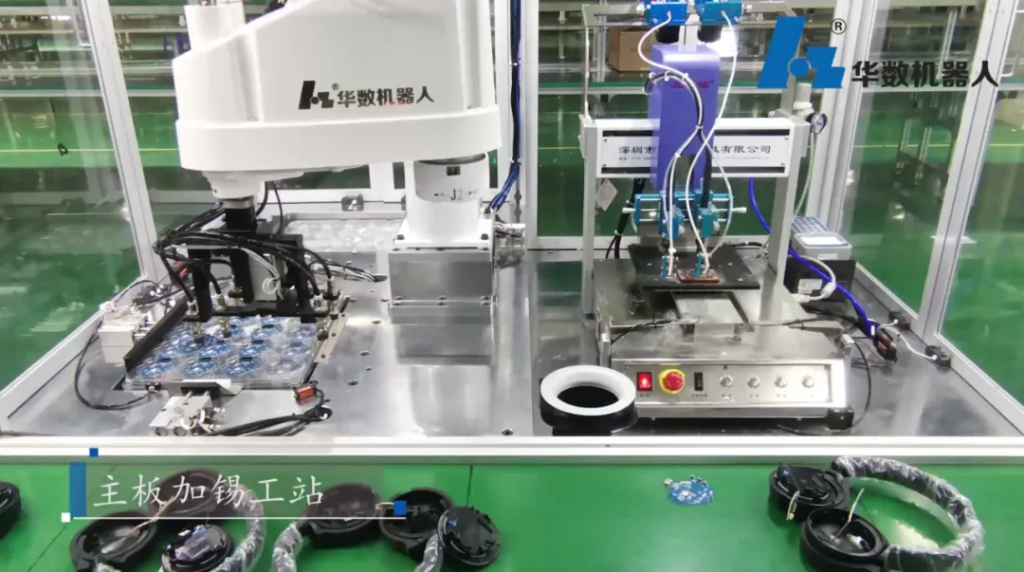
1. Preheat the tin spraying equipment to ensure the wettability of tin and lead.
2. Tin spray treatment: including tin spray drying, cooling, solder layer detection, solder layer correction and other processes.
There are many tinning processes on the mainboard, and manual welding is prone to poor welding, which is not efficient in production activities.
The introduction of the HSR Robot Bluetooth headset production line can improve production efficiency: the robot loading speed is several times higher than manual loading. The robot can work continuously and has stable performance, which can improve the overall production efficiency of the enterprise. Robots for tin loading can improve product quality: during the loading process, as long as the parameters and movement trajectory are given, the actions can be accurately repeated and the parameters are constant, thus ensuring product quality.
02 Screw locking: mainboard locking and screwing station, speaker screwing station
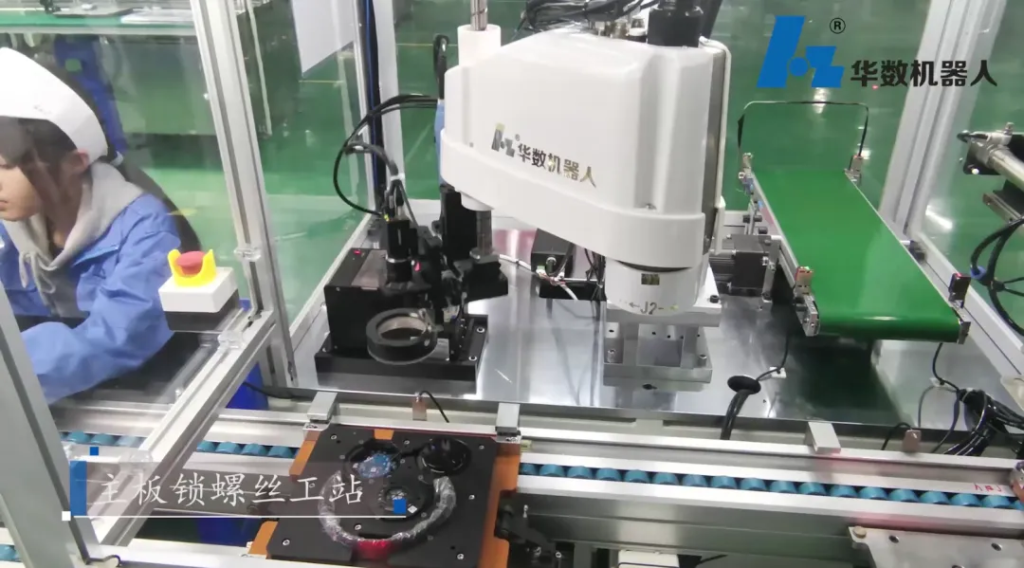

Introducing the HSR Robot Bluetooth headset production line, which integrates automatic picking and placing, automatic locking, and automatic detection. It uses visual cameras for precise positioning, mechanical clamps for mobile transportation, integrated and visual management, and ultimately realizes mainboard locking and speaker locking. process, greatly improving production efficiency and significantly improving the yield rate.
03 Robotic gluing: microphone dispensing station
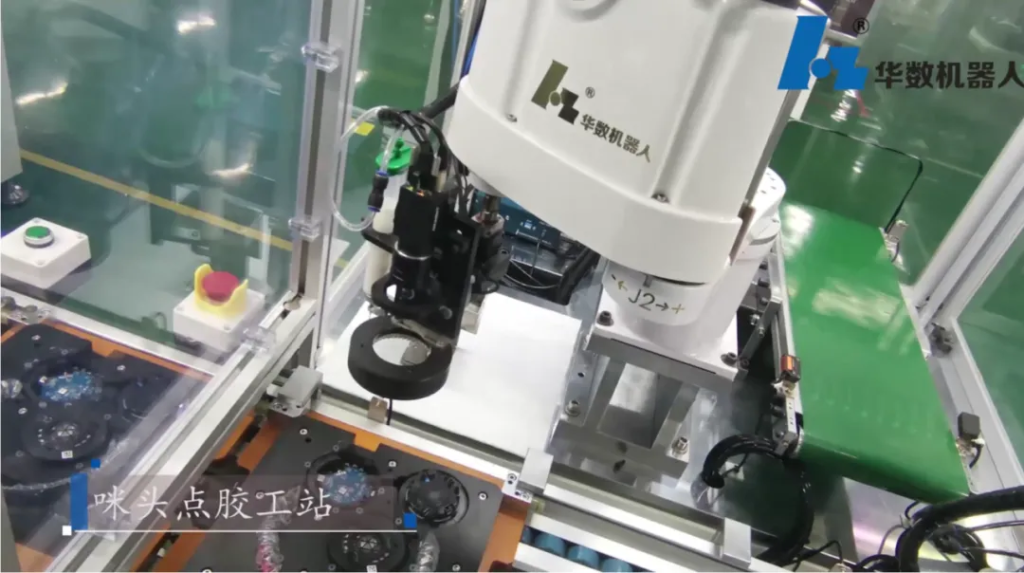
The dispensing path is complex and has many irregular arcs; the requirements for controlling dispensing are high. There are many types of glue used in dispensing. These three points make the dispensing process of Bluetooth headset very time-consuming from material selection to operation, which is not conducive to the efficient production of enterprises.
Introducing the HSR robot earphone production line, the robot dispensing can automatically complete the dispensing operation, improving production efficiency and reducing production time and labor costs. It can accurately control the flow, pressure and speed of glue, ensuring the uniformity and consistency of glue dispensing. Traditional manual dispensing is prone to human errors, while robot dispensing can perform dispensing operations according to pre-set parameters, reducing the possibility of human errors.
04 Robot depalletizing and labeling: destacking blister boxes and labeling SN
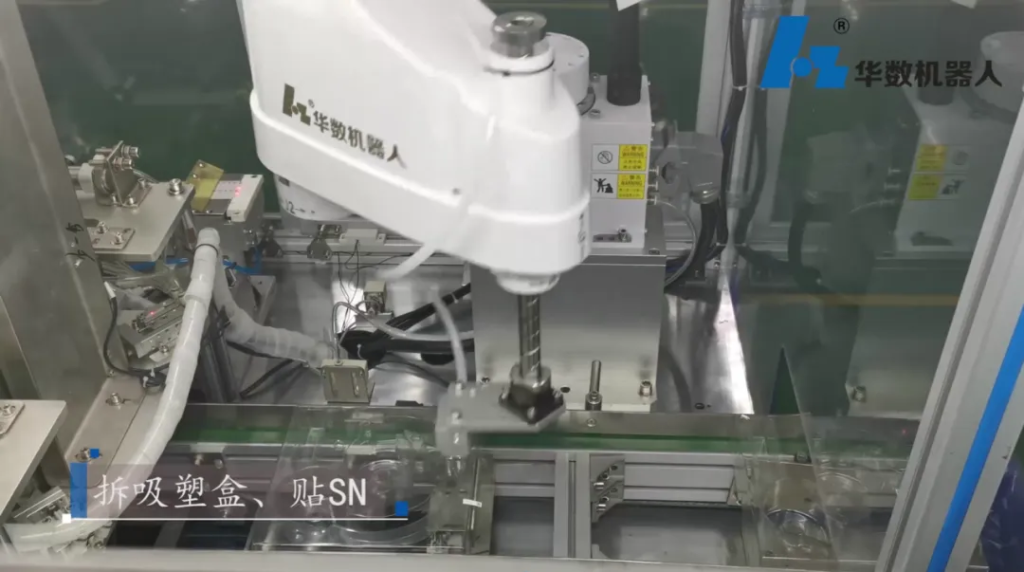
The introduction of robot labeling can accurately paste it at the designated position every time and ensure that the label is firmly pasted: the label is pasted online in real time and verified immediately after being pasted. The operation cycle is short and the efficiency is high.
05 Robot assembly: Light guide column installation station
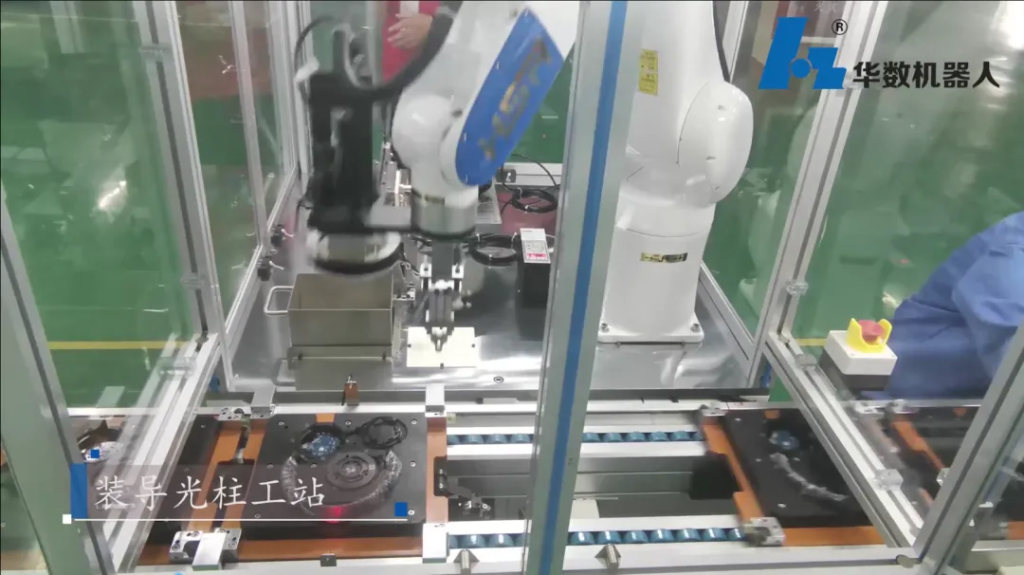
06 Robot packaging: Instructions background is stuck into the carton and wrapped in Sydney paper
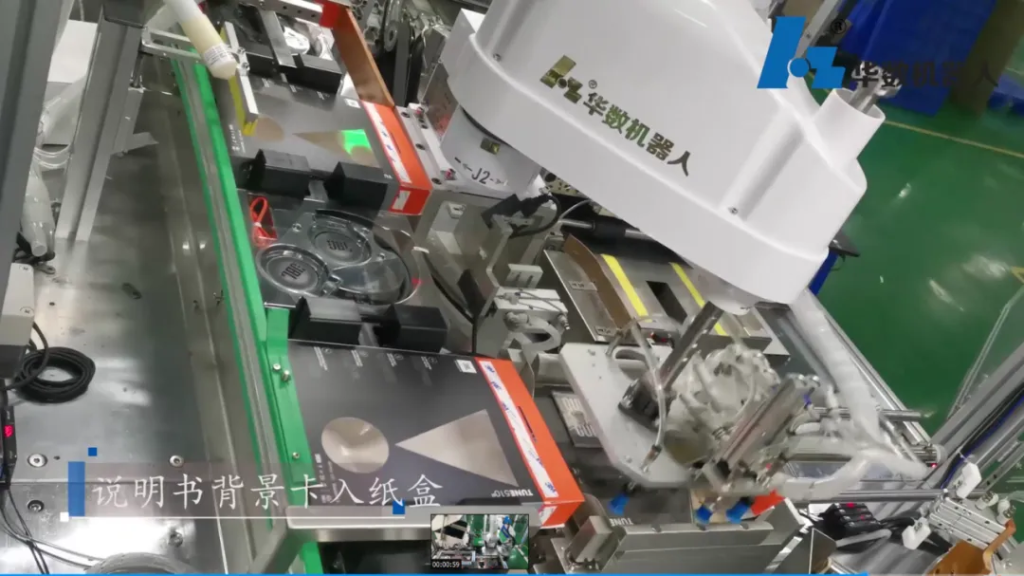
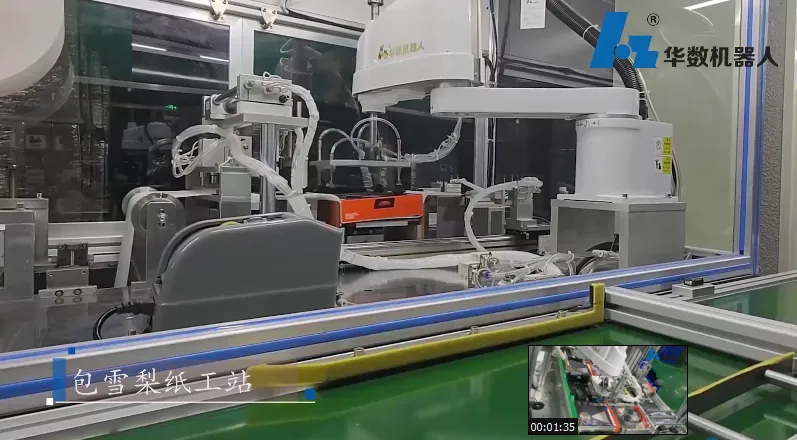
HSR Robot’s Bluetooth headset production line realizes the full-process automated production of Bluetooth headset assembly, functional testing and packaging through the application of industrial robots, machine vision, information perception, flexible intelligent control and other technologies. The production line personnel are reduced to the original number of personnel 48%. At the same time, the production line capacity increased by 47%, the single-hour production capacity exceeded 220pcs/h, the product first-time pass rate increased to 99.5%, and product consistency was significantly improved.
HSR Robot’s Bluetooth headset production line helps enterprises reduce costs and increase efficiency, achieving a successful transformation from labor-intensive production to automated production.
For a long time in the future, Bluetooth headsets will make rapid progress in the electronic product market. Introduce the HSR Robot Bluetooth headset intelligent production line as soon as possible to improve production efficiency and seize the opportunity in the Bluetooth headset market!