Technical application of HNC8 CNC Controller in lathe processing
Automatic chip breaking technology
The automatic chip breaking technology uses the low-frequency reciprocating motion of the cutting axis to form a period of “empty vibration” to achieve fine fragmentation of the chips and remove them intermittently, thus effectively solving the problems caused by entangled iron chips.
Automatic chip breaking technology
The automatic chip breaking technology uses the low-frequency reciprocating motion of the cutting axis to form a period of “empty vibration” to achieve fine fragmentation of the chips and remove them intermittently, thus effectively solving the problems caused by entangled iron chips.
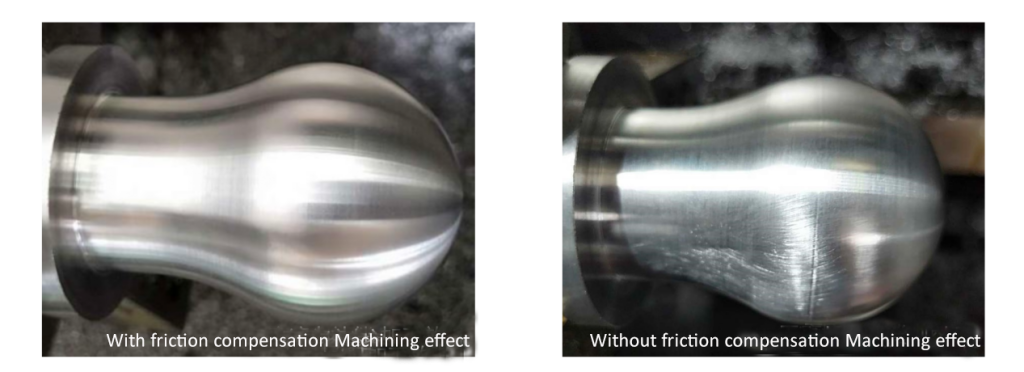
Hardware Current Loop Technology
HuazhongCNC adopts hardware current loop technology, thus significantly improving the response performance of the current loop as well as the stiffness and response speed of the servo control. With the support of this technology, the response speed of the feed servo current has been increased by 30%, which brings better gain and control accuracy and realizes high-precision machining effect.
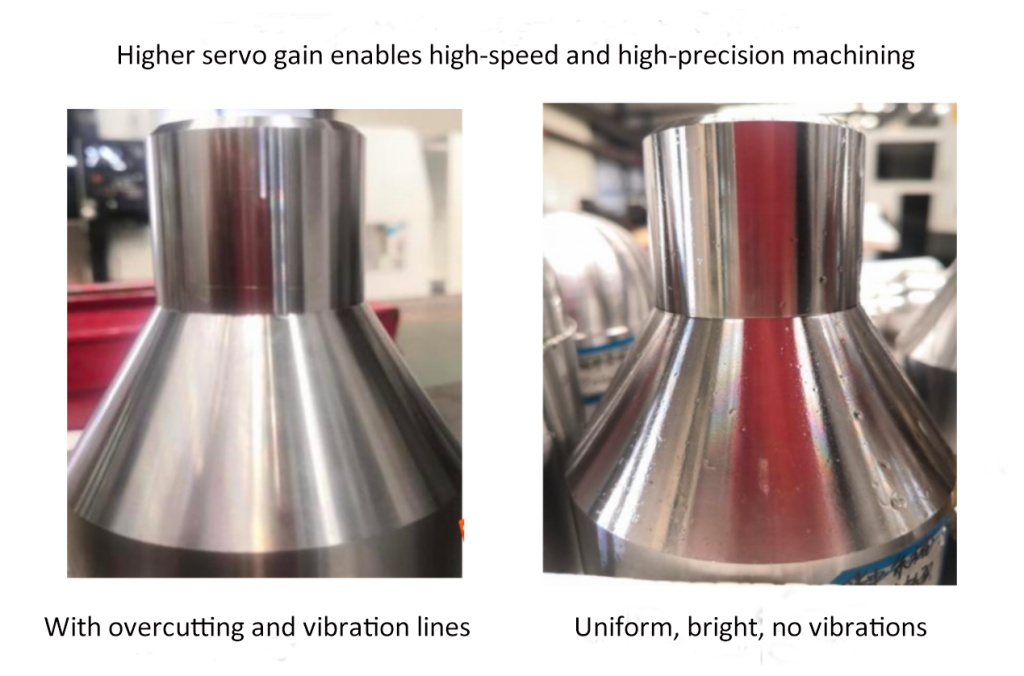
Thermal error compensation technology
Temperature is the main factor that generates thermal error in CNC machine tools. During the operation of the machine, the friction of the motor, bearings and other components generates heat, causing the internal temperature of the machine tool to climb gradually. At the same time, the temperature fluctuation of the working environment of the machine tool will also have a negative impact on its machining accuracy. In order to solve this problem, HuazhongCNC Controller adopts the method of accuracy compensation to correct the accuracy of each component of the machine tool in order to realize the effect of its precision machining.
Servo self-tuning technology
Servo parameter self-tuning technology further calculates and optimizes a set of more ideal servo parameters by accurately identifying the inertia of machine tool moving parts and their interaction relationships. After setting the parameters, starting the self-tuning process with one click can effectively shorten the machine tool debugging time and achieve the best processing status, thereby increasing the machine tool’s processing efficiency by about 15%.
High-speed servo tool change
The acceleration of the servo tool post can reach 1.2G. When the cutter head is in an unloaded state, the adjacent tool change time is 0.179 seconds, and the farthest tool change time is 0.393 seconds; when the cutter head is in a full load state, the adjacent tool change time is 0.180 seconds, the longest tool changing time is 0.4 seconds, which improves the tool changing efficiency by about 20%.
Crankshaft function
HuazhongCNC Controller is equipped with an efficient three-axis following high-speed inspection and repair function. It realizes the crankshaft turning function through precise control of the C-axis servo spindle position and linked interpolation of the X-axis and Z-axis.