Car Welding Robot Applied in the Automobile Welding Automation Field
The production quality requirements of automobiles are becoming more and more stringent, and automobile manufacturers are constantly improving their production efficiency and production quality to meet the increasing demands of people. High and new technologies are continuously applied in the field of automobile manufacturing, such as car welding robots, to meet automobile quality and production efficiency. Automobile manufacturers have introduced welding robots into the field of automobile welding to improve their core competitiveness.
The traditional automobile manufacturing industry has low production efficiency, high labor intensity, poor working environment, and low degree of automation. As a traditional technology and process in manufacturing, welding has developed rapidly. With the development of computer technology, automatic control, numerical control and robot technology, automatic welding robot technology has become increasingly mature. Welding robots not only improve the stability of operation, but also improve welding quality and production efficiency, and improve the operator’s working environment. At present, robots are widely used in the four major production processes of automobile manufacturing, including stamping, welding, painting, and final assembly. Among them, arc welding robots and spot welding robots are the most widely used.
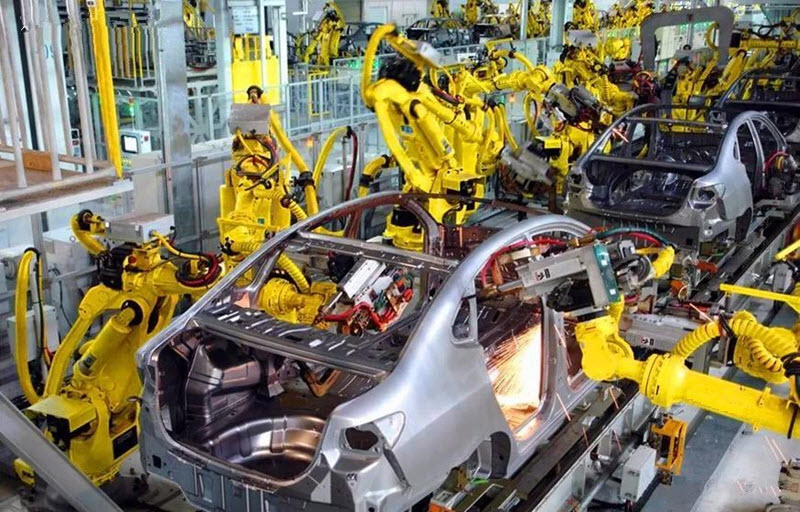
1. Robotic Car Body Welding
Resistance spot welding automobile body assembly welding includes assembly welding of frame, floor, side panels, door and body assembly welding, etc., and resistance spot welding technology is widely used in the assembly welding production process. In the car body manufacturing process, the quality of the welded joints not only directly determines the manufacturing deviation of the body welding assembly process, but also determines the reliability and safety of the car.
In order to meet the needs of diversified production of modern automobile products, improve the automation degree of the body welding production line, reduce the labor intensity of the operator, improve work efficiency, and ensure the welding quality, in the modern body welding production line, spot welding robots are used instead of cumbersome Suspended spot welding machines and spot welding robots are mainly used in repair welding stations for body welding and body assembly welding stations. Moreover, due to the use of spot welding robots, a flexible production method for body assembly and welding has been realized, and mixed-line production of multiple varieties and small batches has been realized.
Application of HNC-RJH605E Robot Used in Car Body Welding Process
In this customer’s application, our RJH605 robot needs to weld 28 points of car body parts, with an average working cycle of 50 seconds. Compared with traditional welding methods, our welding robot has a very high work efficiency, greatly saving labor, and the welding joints have high consistency, beautiful appearance and good quality.
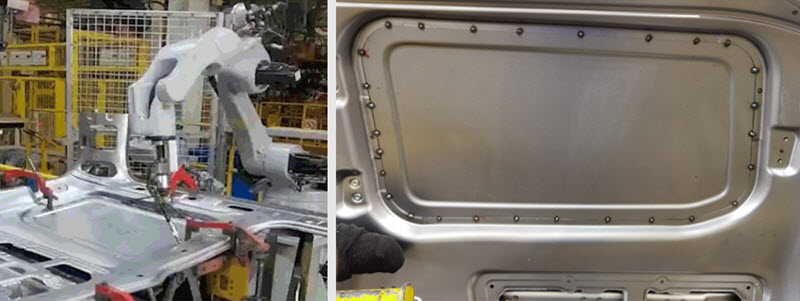
2. Robotic Auto Parts Welding
Spot welding, projection welding, seam welding, butt welding and arc welding are widely used in the production of auto parts. For example: spot welding of beam assembly bracket, projection welding of drive shaft balance sheet, seam welding of automobile fuel tank, continuous flash butt welding of automobile rim, arc welding of automobile steering arm, muffler, etc. In terms of arc welding, the robot is mainly hydraulically driven. It helps the robot to complete the work by setting the working route and moving speed in advance. Similarly, the work done by the robot does not have welding disadvantages under normal circumstances.
Applications of HNC-RJH605 Robot Used in Car Parts Welding Process
Customer 1 – Car Parts Manufacturer in Chongqing, China
In June 2017, HuazhongCNC successfully signed a formal cooperation agreement with an auto parts manufacturer in Chongqing. From wiring to PLC master control and welding process package joint debugging, it took less than one month to complete the master control debugging and welding process debugging, and the vertical welding method was used for the first time.
At present, five work stations can produce five products, and only one welding worker is required to operate it. An average of 400 pieces/station can be welded a day, and the welding capacity can reach 2000 pieces a day. Because the welding consistency is good, it eliminates the need to manually polish the weld, improves production efficiency and work quality, solves the harsh welding environment and the difficult situation of welding workers, and completely eliminates the difficulties of customers.
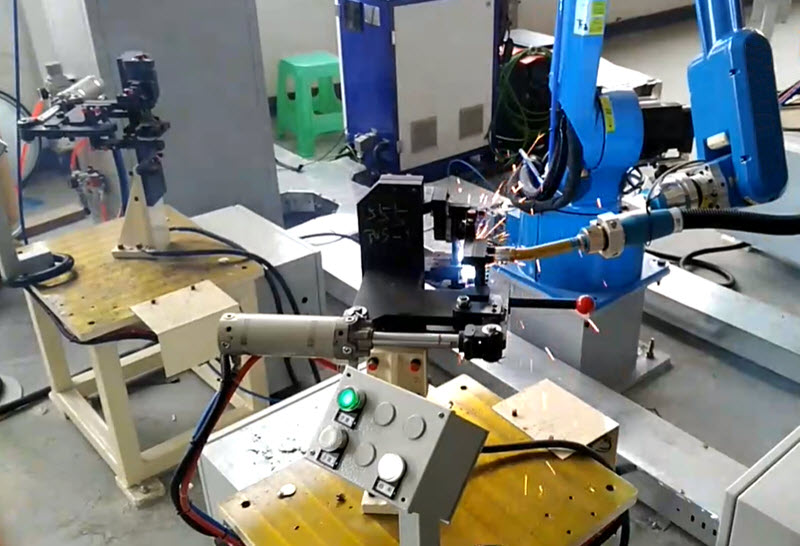
Customer 2 – Auto Parts Manufacturer in Foshan, China
The car parts robotic welding unit is composed of welding robots, welding high-precision tooling fixtures, all-digital industrial welding power supplies, safe and convenient operating systems, and sewage and smoke extraction systems. The whole welding unit is mainly used for welding the parts of the car shift plate. Each batch of tooling fixtures can hold 20 workpieces, 20 working positions form double-sided welding, and the welding seam reaches 40. The customer requires the workpiece to have no spatter on the surface, the welding seam must be at a 45-degree angle, and the welding seam must be uniform. Welding, undercut, collapse, surface pores, surface cracks, burn-through, weld penetration treatment and destructive test are required. In the early stage of welding debugging, low current and low voltage are required for welding, and the weld formation must reach golden blue color.
Each workpiece has two welding positions, and the robot continuously welds. The average welding time to complete a batch of workpieces is about 4 minutes, and the efficiency is much higher than manual welding (the original manual welding is about 5-6 minutes to weld a batch).
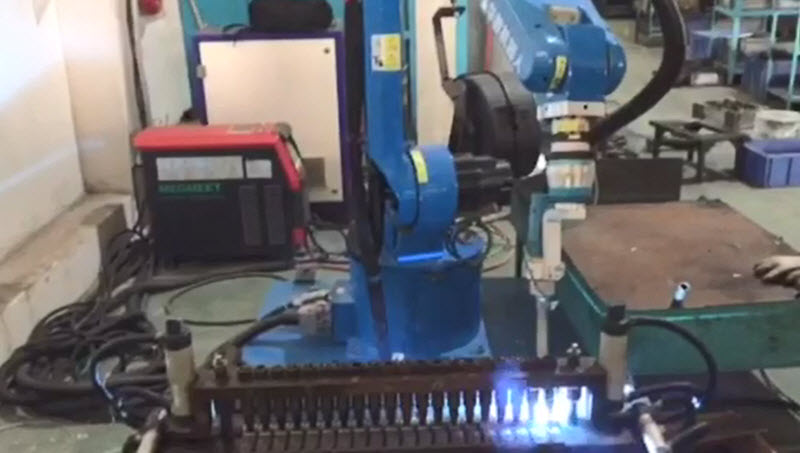
Customer 3 – Welding Workshop of Automobile Parts Manufacturer in China
This auto parts welding unit is a dual-robot dual-station plus positioner scheme design, which uses an extended-arm robot, an imported welding power source and a water-cooled welding torch for welding. The welding process adopts the double-pulse multi-channel method. Compared with manual welding, this method saves half of the working time, and the operation is simple, the welding quality is stable, and the weld seam is beautiful.
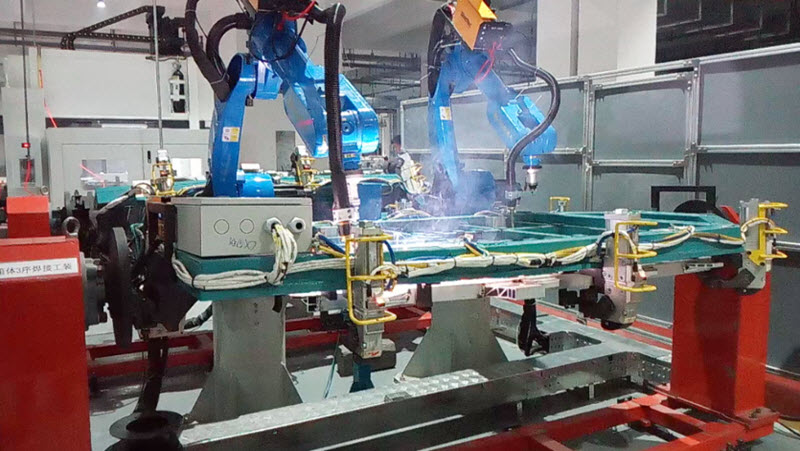