- The laser and Mig welding robot is equipped with an easy-to-use HsPad teaching pendant, which makes it effortless for users to operate.
- It can be connected to industrial Ethernet such Profinet through the gateway device to realize data communication between the controller and external PLC.
- Intelligent trajectory optimization strategy for optimal control performance.
- Integrated with various sensor such as vision sensors, torque sensors, stability sensors and etc. Alert mode and assist mode combined with sensors.
- Based on rich practical cases and integration of processing technology, we have developed a variety of process packages such as welding process packages, which greatly reduces the difficulty of programming.
- RJH615 laser welding robot has double guarantees of performance and stability: the linear trajectory accuracy is as high as 0.08mm and the arc trajectory accuracy is as high as 0.2mm when the speed is 100%.
- It provides remote access monitoring to view the running status of the robot in real time, which is helpful for remote troubleshooting.
- RJH615 Mig welding robot can provide professional and customizable services, so that beginners without welding experience can easily get started.
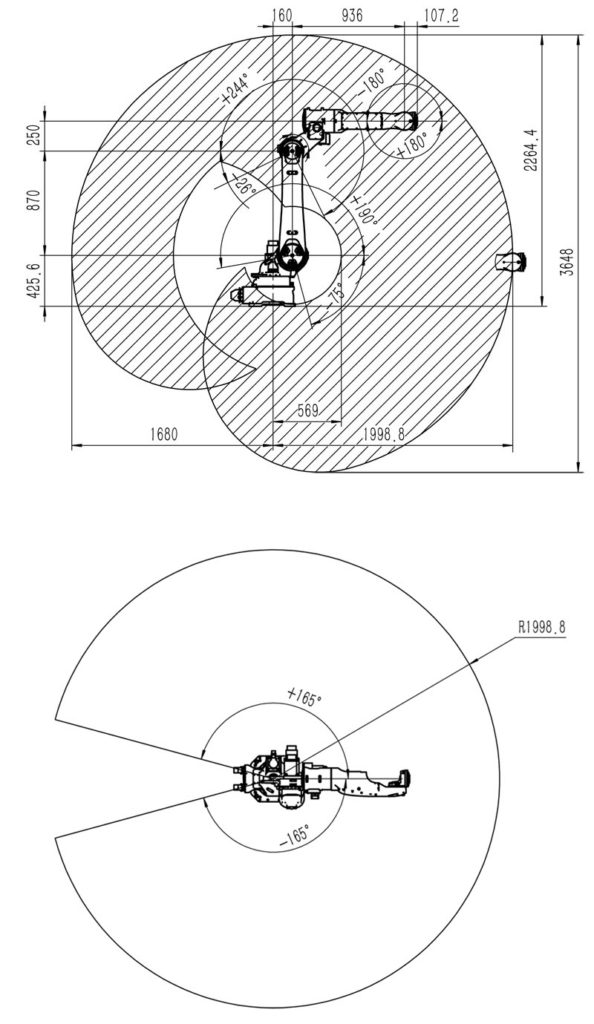